Diabon
The Alfa Laval Diabon® plate-and-frame heat exchangers are used for tough corrosive media. This range of heat exchangers combine Alfa Laval's know-how in heat transfer with Germany based SGL Carbon's expertise in graphite process equipment. Alfa Laval Diabon® gasketed plate-and-frame heat exchanger combines high-efficiency heat transfer benefits with the exceptional corrosion resistance of graphite material.
Alfa Laval and SGL Carbon, Germany, worked together to develop DIABON® plate heat exchangers. This collaborative effort combines Alfa Laval’s plate heat exchanger know-how with SGL Carbon’s expertise in graphite process equipment. The resulting product combines the high-efficiency heat transfer benefits of conventional plate heat exchangers with the exceptional corrosion resistance of graphite material.
DIABON® plate heat exchangers are therefore ideal for handling highly corrosive fluids such as:
- hydrochloric acid and gas in all concentrations
- sulphuric acid up to 90%
- hydrofluoric acid up to 60%
- all concentrations of phosphoric acid
- pickling acids in surface treatment plants
- electrolytes used in the mining industry
- mixed acids
- chlorinated hydrocarbons
- catalysts such as aluminium chloride.
Så fungerar det
Alfa Laval Diabon™ plate heat exchangers function as conventional gasketed plate heat exchangers, except that the plates separating the media are made of special graphite materials. Diabon™ plates are available in three different graphite grades; F100, NS1 or NS2.
The plates are sealed in the plate pack by PTFE rope gaskets resistant to aggressive chemicals and temperatures above 180°C (356°F). At assembly the gasket is flattened to a very thin film of approximately 0.2 mm (0.078”), which secures minimal contact to the corrosive media and long intervals of reliable operation. The gasket can be kept in storage for virtually unlimited periods.
Tightening bolts with springs on the frame compensate for thermal expansion of the plate pack, which minimizes risk of plate cracking.
A combination of high turbulence and counter-current flow offers maximum heat recovery. Two media flow in channels between corrugated plates creating turbulence which results in better heat transfer than alternative shell-and-tube or block alternatives. The counter-current flow allows for close temperature approaches enabling great heat recovery.
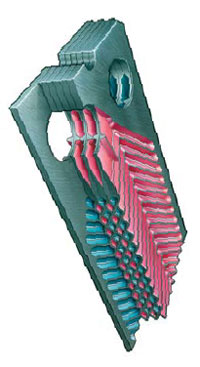